Beginner’s Guide: Forged vs Welded Carbon Steel Pipe Fittings: Which is Better for High-Pressure Systems?
Table of contents
- Preface
- Forged Fittings
- Welded Fittings
- Technical Showdown: Performance Under Extreme Pressure
- Cost vs. Longevity: The Economic Trade-Off
- When to Choose Forged or Welded
- 5-Step Selection Guide for Engineers
- FAQs
- Summarize
Preface
For engineers and procurement teams, choosing between forged and welded carbon steel fittings is not only a matter of cost, but also of safety, compliance, and long-term reliability.
In this article, we will focus on the differences between them and provide some reliable advice for beginners.
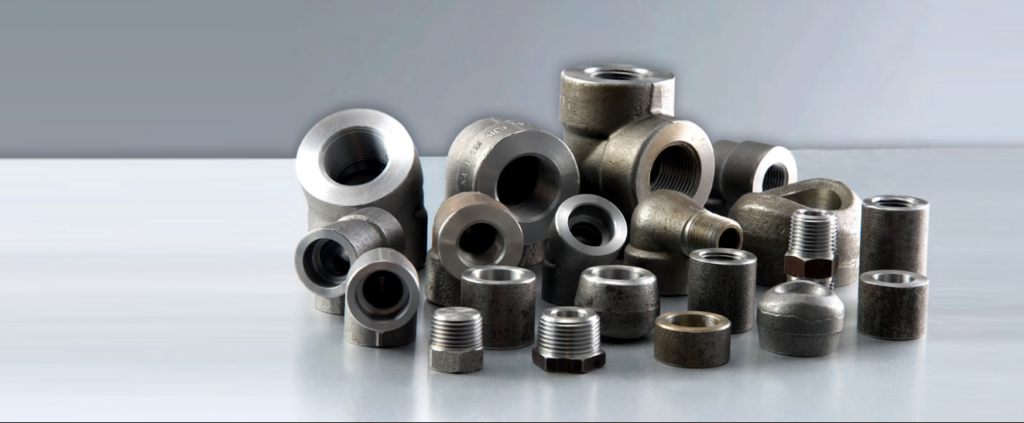
Forged Fittings
Shaped by compressing heated carbon steel billets under extreme pressure, creating a seamless grain structure.
Welded Fittings
Fabricated by welding rolled steel plates or pipes into desired shapes.
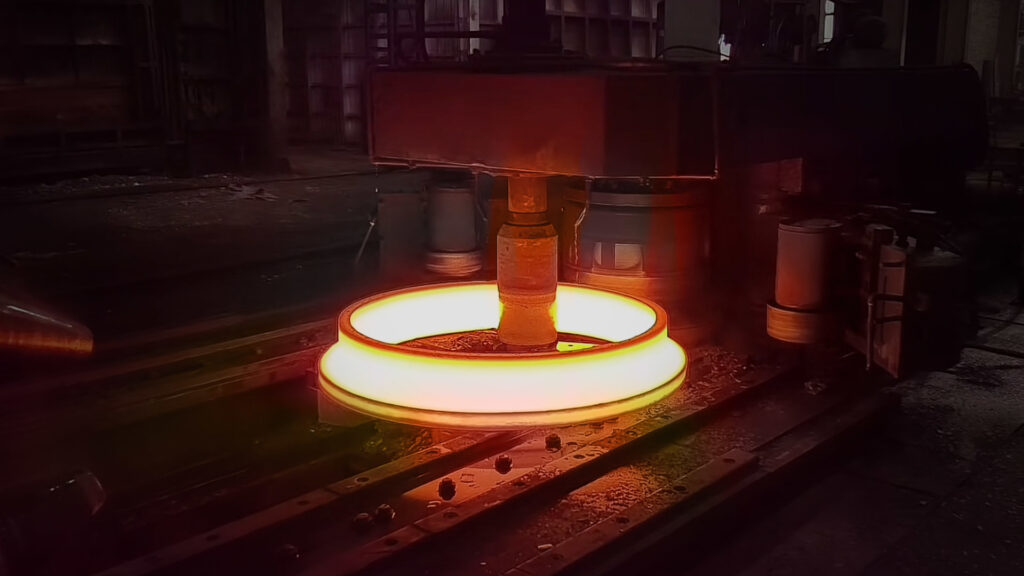
Technical Showdown: Performance Under Extreme Pressure
Pressure Resistance
Parameter | Forged Fittings | Welded Fittings |
Max Pressure | 10,000 PSI (ASME B16.11) | 6,000 PSI (ASME B16.9) |
Burst Strength | 1.5x higher than welded | Vulnerable at weld seams |
Leak Risk | Near-zero (no seams) | Higher at welded joints |
A hydraulic system using forged socket welds withstood 9,500 PSI cyclic loads without failure, while welded counterparts cracked at 5,200 PSI.
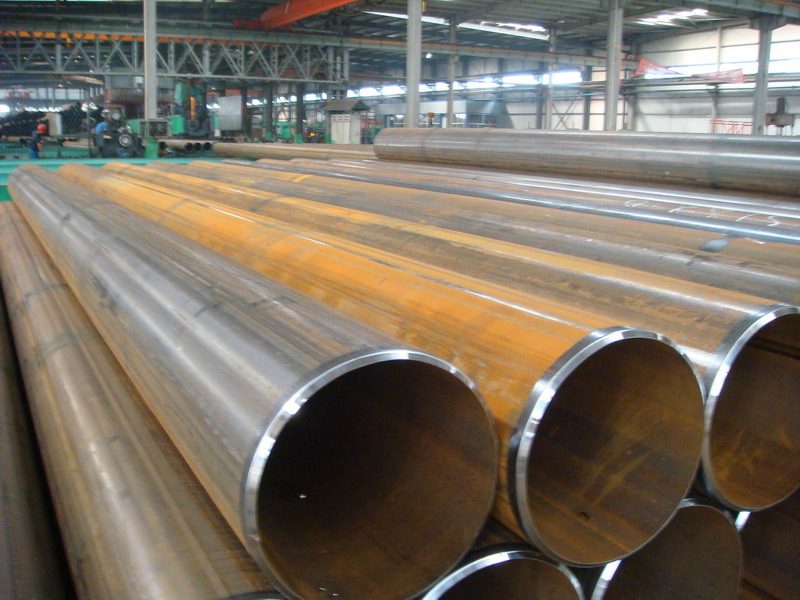
Fatigue and Impact Resistance
Forged Fittings
- Homogeneous grain structure resists crack propagation.
- Ideal for systems with frequent pressure spikes (e.g., oil wellheads).
Welded Fittings
- Heat-affected zones (HAZ) near welds are prone to micro-cracks.
- Unsuitable for vibration-heavy environments (e.g., offshore platforms).
Temperature Tolerance
- Forged: Stable up to 650°C (1,202°F) due to uniform material properties.
- Welded: Limited to 425°C (797°F); welds oxidize and weaken at higher temps.
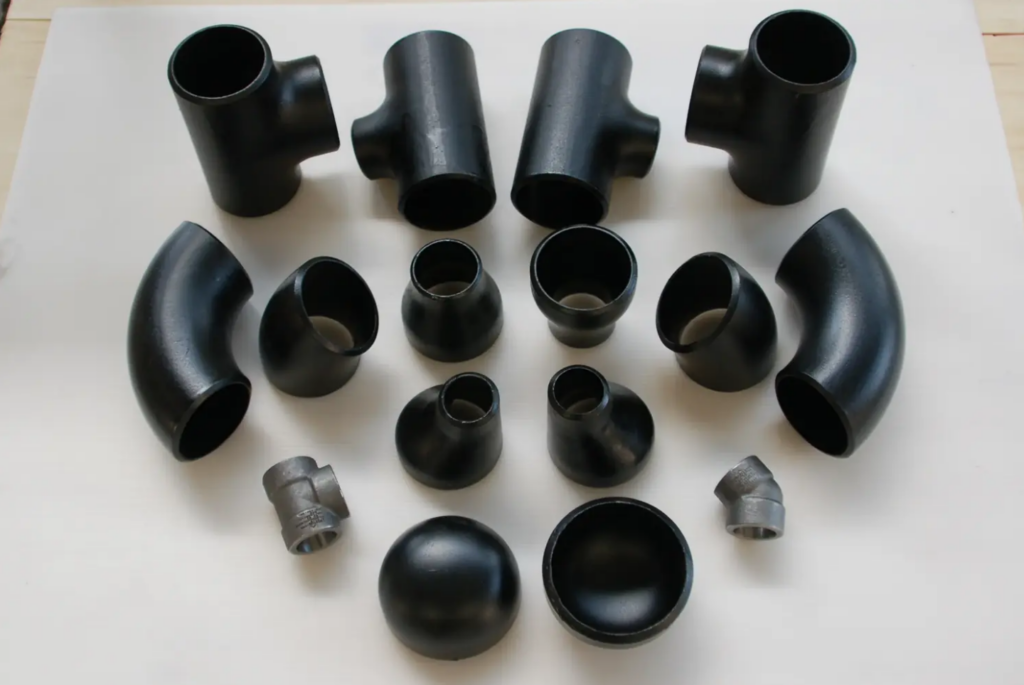
Cost vs Longevity: The Economic Trade-Off
Upfront Costs
- Forged Fittings: 30-50% more expensive.
- Welded Fittings: Cheaper for bulk orders (economies of scale).
Lifetime Value
- Forged:
- 20+ years in high-pressure service with minimal maintenance.
- Example: Offshore oil rigs use forged fittings to avoid costly downtime.
- Welded:
- 8-12 years lifespan; requires annual NDT inspections.
- Total cost of ownership may exceed forged over 10 years.
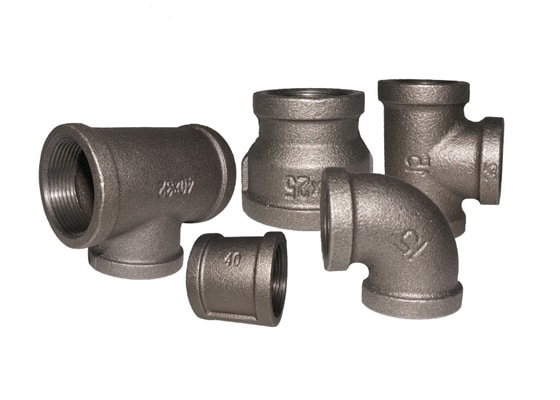
When to Choose Forged or Welded
Forged Fittings Dominate In
- Oil & Gas: Wellhead equipment (API 6A), sour service pipelines.
- Nuclear Power: Reactor coolant systems (ASME III).
- Aerospace: Hydraulic systems in landing gear.
Welded Fittings Suffice For
- Low-Pressure HVAC: Chilled water systems (≤2,000 PSI).
- Water Treatment: Non-corrosive fluid transport.
- Budget-Constrained Projects: Where initial cost outweighs risk.
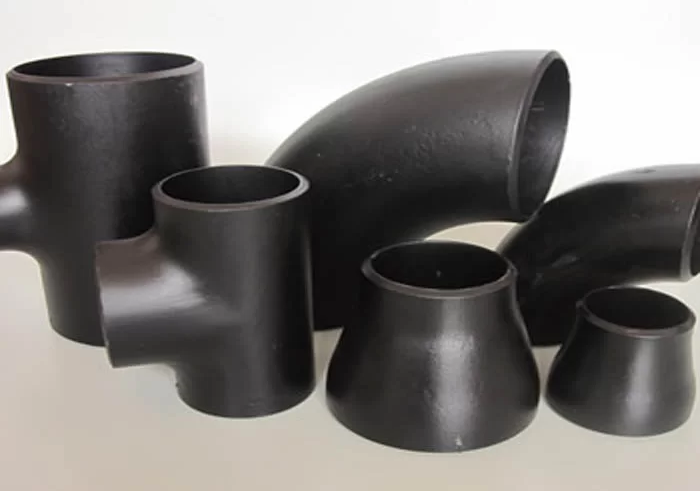
5-Step Selection Guide for Engineers
- Calculate System Pressure: Use ASME B31.3 formulas to determine max operating pressure.
- Assess Corrosion Risks: For corrosive media (e.g., H2S), forged fittings resist pitting better.
- Review Standards:
- Forged: ASTM A105/A182 (ASME B16.11).
- Welded: ASTM A234 (ASME B16.9).
- Audit Suppliers:
- Forged: Require ISO 9001 + PED 2014/68/EU certifications.
- Welded: Demand EN 10204 3.1 mill test certificates.
- Prototype Testing: Pressure-test sample fittings to 1.5x operating load.
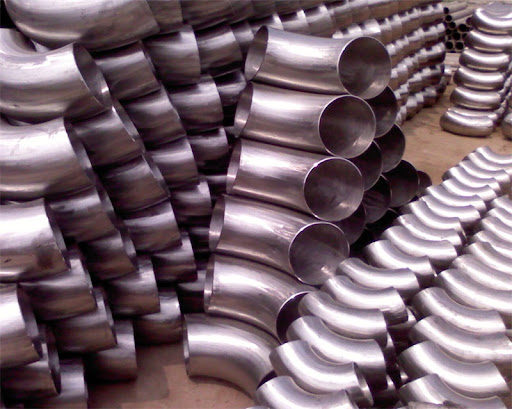
FAQs
Q1: Can post-weld heat treatment (PWHT) improve welded fittings?
PWHT reduces residual stresses but won’t match forged fittings’ integrity. ASME B31.3 mandates PWHT for welds in cyclic service.
Q2: Are threaded forged fittings leak-proof?
Proper thread sealant (e.g., PTFE tape) ensures sealing, but forged threads withstand higher torque than welded.
Q3: How to inspect forged fittings for defects?
Use ultrasonic testing (UT) to detect internal voids or inclusions.
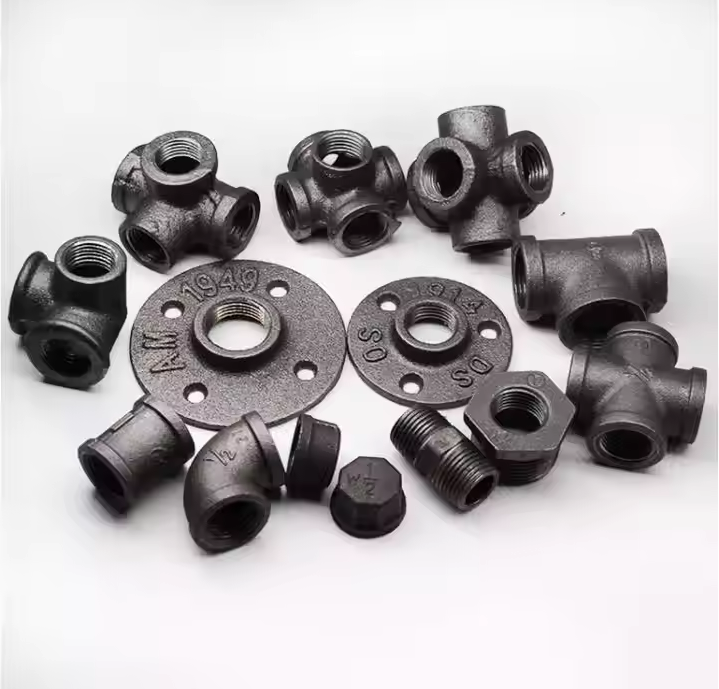
Summarize
This article mainly introduces the difference between forged and welded carbon steel fittings. In high-pressure systems, forged carbon steel fittings are the undisputed champion. While welded fittings suit low-risk applications, critical systems demand the reliability of forged designs.
If this article is helpful to you, please forward it to those in need.
The article is provided by Beijing Metleader Pipeline!